



Linear axes
- Position feedback: linear encoders provide accurate and real-time feedback on the position of the linear axis. This information is essential for the CNC controller to ensure that the tool or workpiece is precisely positioned according to the programmed instructions.
- Closed-loop control: the CNC system utilizes closed-loop control, where the feedback from the linear encoder is continuously compared with the commanded position. Any discrepancies trigger adjustments to the motor movements, ensuring that the actual position matches the desired position.
- Precision machining: the high resolution of linear encoders enables CNC machines to achieve fine positional increments, leading to precise machining operations. This is crucial for producing accurate and high-quality parts.

- Speed control: spindle encoders provide feedback on the rotational speed of the spindle. This information is crucial for maintaining the desired cutting speeds during machining processes. It allows the CNC controller to adjust the spindle speed in real-time to match the programmed parameters.
- Tool synchronization: in multi-tool machining or tool changes, spindle encoders help synchronize the movements of the spindle with the tool change process. This ensures smooth transitions and prevents collisions between the tool and the workpiece.
- Thermal compensation: spindle encoders contribute to thermal compensation by providing feedback on temperature-related changes in the spindle. This information allows the CNC system to adjust the machining parameters to account for thermal expansion or contraction.



- Angular position feedback: rotary table encoders provide feedback on the angular position of the rotary table. This information is critical for applications where workpieces need to be rotated to specific angles during machining operations.
- Indexing and contouring: CNC machines often use rotary tables for indexing or continuous contouring. The feedback from rotary encoders ensures precise angular positioning, enabling the CNC controller to execute complex machining paths and contours.
- Multi-axis coordination: in machines with multiple axes, rotary table encoders contribute to the coordination of movements. The CNC controller uses the feedback from the rotary encoder to synchronize the rotational movements of the table with other linear and rotary axes.


Performance
✔ Scale accuracy
✔ Scale linearity
✔ Resolution
✔ Sub-divisional error
✔ Scale CTE
✔ Speed
✔ Controller input frequency
✔ Cable flex Radius
✔ Cable flex life
Environment
✔ Temperature
✔ Humidity
✔ Vibration
✔ Electromagnetic compatibility (EMC)
✔ IP rating
Installation
✔ Size
✔ Top or side mount
✔ Ride height tolerance
✔ Yaw / pitch / roll
✔ Readhead travel orientation
✔ Cable exit direction
✔ Connectors
✔ Substrate type
✔ Mounting method
✔ Reference datum
✔ Limits
Others
✔ Analogue / digital
✔ Interpolation clock frequency
✔ Alarm type
✔ Reference limit
✔ Termination
✔ Protocol
Heading 1
Lorem Ipsum is simply dummy text of the printing and typesetting industry. Lorem Ipsum has been the industry's standard dummy text ever since the 1500s, when an unknown printer took a galley of type and scrambled it to make a type specimen book.
Form Heading
Enhancing stability in manufacturing high-quality products
Enhancing stability in manufacturing high-quality products

FORTiS encoders are also very easy to install. By viewing the setup LEDs, it only takes us an average of seven minutes to install the encoder on each axis.
Taking the HEAKE LH800 model as an example, the total installation time for the three axes is less than half an hour, which is twice as fast as the time taken with other encoder brands that were tried in the past.
HEAKE Precision Technology Company (Taiwan)
Accelerate the performance of direct-drive motors
Haozhi is an industry leader in direct-drive technology for machine tool and robotics applications in China.
The LA11 was ideal because it minimised our space requirements by producing both absolute and incremental signals from one readhead and scale tape.
Haozhi Mechanical and Electrical (China)
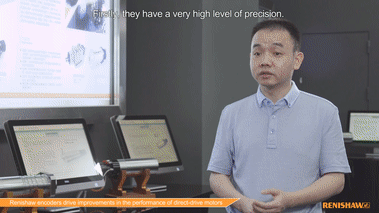
Breakthrough in multi-axis rotary table design
As multi-axis machine tool technology matures, demand for rotary tables with enhanced accuracy and rotational speed is rising.
Taiwan's Industrial Technology Research Institute (ITRI) has addressed this market trend by developing an advanced dual-axis rotary table with integrated RESOLUTE absolute rotary encoders and Panasonic serial communication protocols for direct interfacing with Panasonic drives and controllers.
Although machine tool environments are generally contaminated with metal swarf, oil and coolant, enclosing an open encoder within the motor eliminates any related problems.
Moreover, RESOLUTE's high level of ingress protection (IP64) provides further assurance.
Industrial Technology Research Institute (Taiwan)

Breakthrough in multi-axis rotary table design
Taiwan's Industrial Technology Research Institute (ITRI) has addressed the market trend by developing an advanced dual-axis rotary table with integrated RESOLUTE™ absolute rotary encoders and Panasonic serial communication protocols for direct interfacing with Panasonic drives and controllers.
Although machine tool environments are generally contaminated with metal swarf, oil and coolant, enclosing an open encoder within the motor eliminates any related problems.
Industrial Technology Research Institute (Taiwan)

Sweet spot between cost control and technology advancement
SOLPOWER is a Taiwanese manufacturer of direct-drive (DD) rotary tables, integrated spindle motors and linear motors. Manufacturing cost control is vital to success in the machine tool industry in Taiwan.
We developed the most cost-effective rotary table possible, which means that cost must be strictly controlled from design, parts procurement to production.
Renishaw as a major supplier is an important part of our cost-efficiency strategy.
SOLPOWER (Taiwan)
For machine tools
Paint Point #1
Paint Point #1
Paint Point #1
Paint Point #2
Paint Point #2
Paint Point #2
Paint Point #3
Paint Point #3
Paint Point #3
The true-absolute encoder with a high-speed fine-resolution position measurement system. Position is acquired immediately on start-up without requiring any motion, offering smooth velocity control and dependable positional stability. Available with linear and rotary scales with a variety of serial interfaces.
✔ High speed
✔ Excellent dirt immunity
✔ Low SDE
✔ Low jitter


The next-generation enclosed absolute encoder is built for use in harsh environments, which delivers high performance and significant benefits over conventional systems with an exceptionally robust enclosed design.
✔ Industry-proven position measurement
✔ Superior sealing
✔ Easy installation
✔ Non contact
LA12 absolute magnetic encoder
Designed for motion control applications as a position and velocity control loop feedback element. LA12’s readhead is sealed to IP67 providing reliable operation with resolutions up to 0.244 µm and supports Mitsubishi, Yaskawa and Fanuc serial communication.
✔ W
✔ D
✔ H
✔ R
AM8192B rotary magnetic encoder IC
Integrates proven filtering optics and interpolation technology into a super-compact, analogue or digital incremental open optical encoder, with wide installation tolerances and built-in calibration functions.
✔ Wide installation tolerances
✔ Dirt immunity
✔ High performance
✔ Robust
OnAxis™ encoder modules
Integrates proven filtering optics and interpolation technology into a super-compact, analogue or digital incremental open optical encoder, with wide installation tolerances and built-in calibration functions.
✔ Wide installation tolerances
✔ Dirt immunity
✔ High performance
✔ Robust
Speak to out manufacturing consultants
Looking for a deeper dive into success stories?
Seeking a tailored solution?
Tell us your requirements and our application engineers will work with you to find the right solution.

Learn how much manufacturers are benefitting from using XK10
Lorem ipsum dolor sit amet, consectetur adipiscing elit. Vestibulum consequat mauris eu ullamcorper convallis. Phasellus accumsan, massa in ultrices eleifend, orci nibh commodo nisl, sed sollicitudin arcu urna sit amet enim. Mauris ante turpis, imperdiet eget interdum ac, eleifend volutpat lacus. Integer id nisi cursus, suscipit dui at, auctor ipsum. Suspendisse pulvinar aliquam sapien, id placerat sem tristique vel.
Video #1
Video #2
Video #3
Case Studies
Lorem ipsum dolor sit amet, consectetur adipiscing elit. Vestibulum consequat mauris eu ullamcorper convallis. Phasellus accumsan, massa in ultrices eleifend, orci nibh commodo nisl, sed sollicitudin arcu urna sit amet enim. Mauris ante turpis, imperdiet eget interdum ac, eleifend volutpat lacus. Integer id nisi cursus, suscipit dui at, auctor ipsum. Suspendisse pulvinar aliquam sapien, id placerat sem tristique vel.