







Performance
✔ Resolution
✔ Rotary range
✔ Sub-divisional error
✔ Controller input frequency
✔ Speed
✔ Readhead mass
✔ Cable flex radius
✔ Cable flex life
Environment
✔ Temperature
✔ Humidity
✔ Vibration
✔ Electromagnetic compatibility (EMC)
✔ Cleanliness (particle, fluid)
✔ IP rating
✔ Vacuum / exposure to X-ray radiation / lighting
Installation
✔ Size
✔ Ride height tolerance
✔ Yaw / pitch / roll
✔ Connectors
✔ Cable extension
✔ Mounting method
Others
✔ Analogue / digital
✔ Interpolation clock frequency
✔ Reference limit
✔ Protocol
Heading 1
Lorem Ipsum is simply dummy text of the printing and typesetting industry. Lorem Ipsum has been the industry's standard dummy text ever since the 1500s, when an unknown printer took a galley of type and scrambled it to make a type specimen book.
Form Heading
Universal Robots - the role of AksIM™ in maximising robot performance
Universal Robots (UR) is one of the most successful, high-profile robot manufacturers in the market. Its multi-axis collaborative robots employ the AksIM™ series magnetic rotary absolute encoder which offers outstanding performance, system safety and stability.

The AksIM™ series magnetic rotary encoder is attached to the reducer's end to directly monitor the actual rotating angle of the UR robot's joint. Compared to some of the robot designs where the encoder is attached to the reducer's front, this approach eliminates system error, resulting in a robot repeatability of ±0.1 mm. UR robots achieve a significant enhancement in overall performance.
The AksIM™ encoder has an outstanding performance specification to satisfy the most demanding robotic application requirements. Resolution is up to 20 bit, with system accuracy up to ±0.1° and repeatability better than the unit of resolution. It features excellent dirt immunity with an IP64 rating to allow operation in harsh industrial environments.
Biped robot control - a quest for balance
One of the challenges for PAL Robotics was maintaining balance while walking, which humans take for granted. There are strict space and weight constraints in the design of joints for humanoid robots to keep robot volumes and inertias as low as possible.
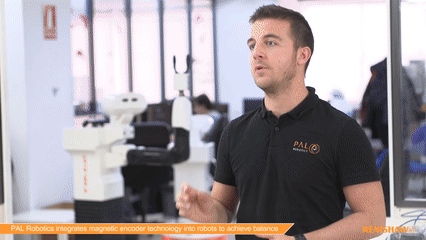
To keep balance is a difficult task as we use reduction gears that introduce some elasticity or non-linearity; so for us, it's really important to get both the position of the motor and position of the joint.
PAL Robotics (Spain)
High-quality encoder feedback is required for the servo-control of each joint in terms of applied torque, velocity and position. Non-contact magnetic encoders, including the AksIM™ and Orbis™ non-contact magnetic encoders, were integrated into knee, wrist and elbow joints of the robot.

Exoskeleton - aid mobility for spinal cord injury (SCI) patients

Precise control of joint angles is required to ensure pilot stability and safety, and this is achieved by using position feedback from high-quality rotary encoders.
Renishaw and RLS did not try to sell us something we did not need. They thought about what it is that we needed and how they could help us with that.
Project MARCH (The Netherlands)
Renishaw and RLS did not try to sell us something we did not need. They thought about what it is that we needed and how they could help us with that.
Project MARCH (The Netherlands)

Self-balancing robotic vehicle
Engineering students from Tokyo Denki University were tasked with solving the classic 'inverted pendulum' control theory problem. The challenge is to create a two-wheeled, self-balancing robotic vehicle.
To achieve the required level of motion control performance, a high-resolution position encoder was a crucial part to enable monitoring and regulation of the motor output. It also had to be small and light enough to be accommodated within the vehicle's slim vertical structure.

Exoskeletons - reliable feedback even after a power failure
Exoskeletons can give those with physical disabilities the potential to stand, move and interact with their environment. These complex robotic systems must have a lightweight and compact structure and they must be easy - even for physically weakened patients - to use, and all while implementing a physiologically complete biomechanical model.
We needed encoders that met our performance criteria without adding excess weight and volume, as any excess in the structure could be detrimental to the user's mobility and might hamper the walking movement.
Marsi Bionics (Spain)
For electric vehicles (EVs)
Paint Point #1
Paint Point #1
Paint Point #1
Paint Point #2
Paint Point #2
Paint Point #2
Paint Point #3
Paint Point #3
Paint Point #3
A non-contact high-performance off-axis absolute rotary encoder designed for applications with limited installation space. The compact, low-profile readhead detects and evaluates the magnetic field of a thin, axially magnetised ring.
✔ True absolute
✔ Improved repeatability
✔ Built-in self-monitoring
✔ Immunity to external magnetic fields

An through-hole rotary encoder suitable for applications where a typical encoder cannot be mounted at the end of the rotating shaft due to space constraints. The through-hole measuring principle allows customization, with various board and magnet sizes to suit your application.
✔ True absolute encoder
✔ Fixable mounting along the shaft
✔ Optional self-calibration
✔ Wide installation tolerances


A compact, super small high-speed rotary magnetic encoder designed for use in harsh environments. The noncontact two part design removes the need for seals or bearings ensuring longterm reliability and simple installation.
✔ Miniature
✔ Non-contact, frictionless design
✔ Industry standard analogue sinusoidal, incremental, SSI and linear voltage output formats
✔ RoHS compliant
The true-absolute encoder with a high-speed fine-resolution position measurement system. Position is acquired immediately on start-up without requiring any motion, offering smooth velocity control and dependable positional stability. Available with linear and rotary scales with a variety of serial interfaces.
✔ High speed
✔ Excellent dirt immunity
✔ Low SDE
✔ Low jitter


An extremely robust absolute linear cylindrical encoder system designed to be integrated into the servomechanism as a transducer, providing accurate measurements with excellent resolution and repeatability.
✔ Built-in self-monitoring
✔ Integral bearings
✔ Small footprint
✔ Suitable for highly dynamic control loops
Speak to out manufacturing consultants
Looking for a deeper dive into success stories?
Seeking a tailored solution?
Tell us your requirements and our application engineers will work with you to find the right solution.

Learn how much manufacturers are benefitting from using XK10
Lorem ipsum dolor sit amet, consectetur adipiscing elit. Vestibulum consequat mauris eu ullamcorper convallis. Phasellus accumsan, massa in ultrices eleifend, orci nibh commodo nisl, sed sollicitudin arcu urna sit amet enim. Mauris ante turpis, imperdiet eget interdum ac, eleifend volutpat lacus. Integer id nisi cursus, suscipit dui at, auctor ipsum. Suspendisse pulvinar aliquam sapien, id placerat sem tristique vel.
Video #1
Video #2
Video #3
Case Studies
Lorem ipsum dolor sit amet, consectetur adipiscing elit. Vestibulum consequat mauris eu ullamcorper convallis. Phasellus accumsan, massa in ultrices eleifend, orci nibh commodo nisl, sed sollicitudin arcu urna sit amet enim. Mauris ante turpis, imperdiet eget interdum ac, eleifend volutpat lacus. Integer id nisi cursus, suscipit dui at, auctor ipsum. Suspendisse pulvinar aliquam sapien, id placerat sem tristique vel.